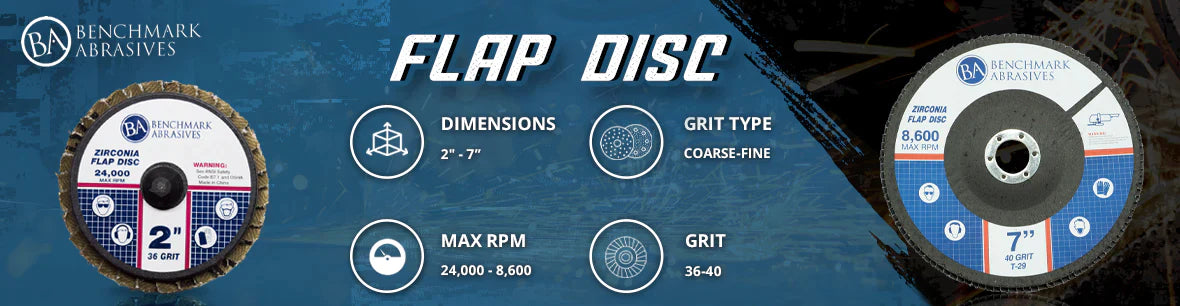
Flap Discs
-
4-1/2" x 7/8" T27 Flap Disc for Aluminum with Stearate Coating - 1 piece
Original price $0.00 - Original price $0.00Original price $0.00$2.82$2.82 - $2.82Current price $2.82| /5.0 / 5.0
37 Reviews
Product Specification Shipping Refund Product Specification 4-1/2" X 7/8" T27 FLAP DISC FOR ALUMINUM WITH STEARATE COATING - 1 PIECE 4-1/2" x 7/...
View full detailsOriginal price $0.00 - Original price $0.00Original price $0.00$2.82$2.82 - $2.82Current price $2.82| /
What are Flap discs?
Flap discs? More like grinding wheels with power steering. These discs up your grinding game by combining the material removal of a conventional grinding wheel with the control of a palm sander. The different abrasive grain sizes allow for a range of different finishes/scratch patterns and the cushion effect of the layered coated flaps allows for a lighter touch for feathered sanding or an aggressive metal hog. The pressure you apply dictates the aggressiveness of the disc.
What makes a flap disc…a flap disc?
There are 3 main components that make up a flap disc; abrasive flaps, hard backing and glue
- Coated Abrasive Flaps – layers of overlapping coated abrasive cloth are applied to a hard backing (metal, plastic or fiberglass) via a thermosetting phenolic resin (or glue). The abrasive flaps provide a cushion effect allowing the user to feather the grinding or bear down on the disc and really remove some material.
- Hard Backing – flap discs can be found with three different backing types (metal, plastic and fiberglass). The metal backed flap discs are not popular and are not commonly found in the US market. Fiberglass backed flap discs are the most common disc you will find. The fiberglass backing is coated in resins that harden under heat and pressure, leaving you with a rigid and lightweight backing to adhere the flaps to. The plastic backed flap discs have become more popular in the past few years with the design of a trimmable edge disc which can be cut back to expose more flap material.
- Glue – The stuff that holds it all together. A thermosetting resin (or glue) that liquifies under high heat, then cures to a hard rock like thickness. The glue holds the flaps firmly to the backing.
What do T27 and T29 mean?
T27 and T29 refer to the type, or shape of your flap disc. They are also commonly referred to as type 27 and type 29. T27 are flat and T29 are conical (or angled).
T27 – Type 27 flap discs are designed with a flat face. These discs are perfect for grinding on flat surfaces like fence posts or gates & risers. The flat face allows the user to bring the disc straight down on the work piece to ground down the protrusion. The ideal angle us of use for this type is 0 to 15 degrees for optimal flap usage.
T29 – Type 29 flap discs are designed with ergonomics in mind. The angled face allows for better, more ergonomic grinding and maximum flap usage when grinding a flat linear plane like grinding down bead weld. The ideal angle us of use for this type is 15 to 25 degrees for optimal flap usage.
…But What about the Curved Ones?
Curved – the latest addition to the flap disc shapes, “curved”, doesn’t come with a type or # call out. They are specially designed for grinding fillet welds and getting into other tighter radius. You may also hear them referred to as Fillet Weld Flap Discs
What’s the Difference Between AO, Zirconia, Ceramic and Surface Conditioning?
Aluminum Oxide (AO) – Aluminum Oxide is the most commonly used grain at an economical price point. Great for use on ferrous metals, composite materials, wood, plastics, and other metals. It features good abrasion resistance, anti-static and anti-clogging.
Zirconia – Zirconia grains have a self-sharpening property and stand up to higher heat and pressure than Aluminum Oxide (A/O), thus making Zirconia the go-to option, providing excellent stock removal that gives you more bang for your buck. They are designed for use on ferrous metals, composite materials, wood, plastics, and other metals.
Ceramic – Ceramic grains micro fracture to allow a continuous supply of the sharpest cutting edges. It's also self-cooling which makes it great for stainless steel and high alloy materials. The lower grits hog up metal for lightning-fast stock removal and the longest cutting life available. They are the best option for mild and carbon steel, stainless steel, cobalt, chrome, Inconel, and titanium applications.
Surface Conditioning – Suitable for a multitude of applications, especially when finishing, blending, removing color from your work surface and light deburring applications. The fiber and resin are also waterproof so these belts can be used both in wet or dry applications.
Flap Discs for Aluminum & Non-Ferrous Metals – These flap discs excel on soft metals like aluminum. They don't gum up like a regular zirconia or aluminum flap disc. The stearate coating, which gives the flap disc its silver color, will liquefy under heat and provide a protective coat on the flaps that prevent loading/gumming up on soft metals.
Felt – While felt is technically not a grain, we do offer a special wool felt flap disc for ultimate polishing. Available individually or in one of our buffing kits.
Regular vs Jumbo (aka High Density) Flap Discs
Regular density flap discs are our signature formula product, designed for both the professional grinding every day or the occasional user. For users looking for a longer life disc, we suggest the high density or Jumbo flap discs which contain 40-50% more flap content. More flaps = longer life.
What Grit Should I Be Using?
Available grits:
AO – 40 grit through 120 grit
Zirconia – 40 grit through 120 grit
Ceramic – 36 grit through 120 grit
Surface Conditioning – 120 through 320 grit
Stearate Coated Discs for Non Ferrous Metals – 36 and 60
Grit size determines the aggressiveness of the flap disc. The smaller the number the more aggressive the grain is, the larger the number the less aggressive it is. Grits 24-40 are generally considered aggressive material removers; 60-80 grits are for medium material removal and grits 120+ are all in the light material removal/finishing category.
If you are unfamiliar with the difference in each grits aggressiveness, we recommend grabbing a scrap piece of metal and a few different grits to start off with. Start with the smaller more aggressive grit and work your way up the grit scale to get a good feel for how they each perform. Once you’ve done that you’ll be ready for any project you pick.
What Size Disc Should I be Using?
The flap disc size will be determined by the tool being used. Benchmark Abrasives carries 2” and 3” flap discs for die grinders/drills and 4”-7” flap discs for use on angle grinders. Make sure to match the size of the disc to your machines RPMs. Operating a 7” flap discs on a 4.5” machine is not safe and could result in injury.
What If I Don’t Have an Angle Grinder?
No grinder, no problem! Benchmark now has a full line of Quick-Change Flap Discs, available in both type 27 and curved (fillet weld) styles. These discs are designed with a hard plastic backing that has a roll lock (type R) or quick-change attachment. You can use these discs on die grinders, drills or any other tool designed to work with quick change discs.
FAQs
How should I store my flap discs?
Keep them in a dry, cool place away from direct sunlight and moisture. Treat them like your favorite six-pack; store them properly, and they'll treat you right when you need them.
Any safety tips for using flap discs?
- PPE is a must: Safety glasses, gloves, and hearing protection.
- Inspect before you wreck: Check the disc for damage before each use.
- Mind the speed limit: Stay within the recommended RPMs.
Remember, safety isn't just a suggestion unless you enjoy unexpected trips to the ER.
Why is my flap disc wearing out so quickly?
Could be excessive pressure, wrong angle, or using the wrong disc for the material.
How do I prevent clogging when working with softer metals?
Use discs designed for non-ferrous metals and apply less pressure. Just like dancing, sometimes a lighter touch gets better results.
Is it safe to exceed the recommended RPM of a flap disc?
Nope. Exceeding the RPM is like redlining your old pickup—you're just asking for trouble.
What's the lifespan of a typical flap disc?
Depends on usage, material, and technique. With proper use, they can last quite a while, but abusing will reduce the lifespan significantly.
Any tips for maximizing flap disc performance?
- Use the right angle: 15-25 degrees is usually ideal.
- Let the disc do the work: Don't press too hard.
- Keep it clean: Regularly check for