
The Art Of Deburring: Techniques and Tools For Smooth Edges
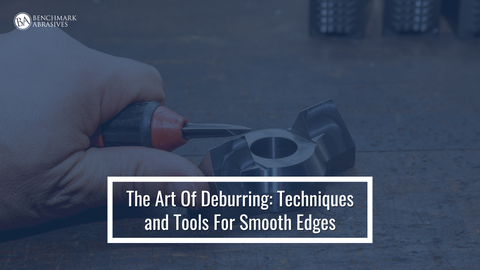
Metal components are widely employed in many industries, including aerospace and automotive. These parts may develop burrs—rough surfaces and sharp edges—during the production process, which will lower their overall quality and performance.
The purpose of the critical deburring stage in the production process is to guarantee smooth surfaces by getting rid of these undesirable burrs. In this blog post, we will discuss deburring, its significance, several deburring techniques, and the tools utilized in this process.
DEBURRING: KNOWING THE FUNDAMENTALS
HOW DOES A BURR FORM - WHAT IS IT?
In the process of the machine cutting or shaping metal parts, the material is removed by the cutting tool in order to form the desired shape. Nevertheless, burrs—which are tiny ridges or sharp edges of undesired material that stick to the metal surface—can frequently emerge as a result of this cutting process.
In several machining processes, burrs frequently form, mainly when working with sheet metal or machined parts. Burrs have a number of detrimental effects on the part's quality. They may make assembly more complex, present safety risks, impair the part's functionality, or even detract from the product's overall visual appeal. In order to guarantee the metal part's quality and functionality, burr removal is a crucial step.
WHY DEBURRING IS IMPORTANT?
In order to create smooth edges and surfaces, metal objects must be deburred. It is an essential stage in the production process since it makes the part much better. The metal part's overall functionality and performance can be improved by eliminating these sharp burrs, guaranteeing a high-quality finish.
Deburring is a critical component of improving the product's aesthetics. The part is more aesthetically pleasing to consumers and users when it has smooth surfaces and edges.
Additionally, removing burrs removes possible safety risks because operators and end users won't be harmed by sharp edges that could cause accidents or injuries.
VARIOUS TECHNIQUES FOR DEBURRING
Deburring can be done in a number of ways, each appropriate for a particular kind of burr or material. Let's examine some of the methods that are most frequently employed in the field:
1. DEBURRING BY HAND
Using hand tools to remove burrs is manual deburring, one of the earliest and most basic methods of deburring. In small shops or for small parts where automation could be more practical, this technique is frequently utilized.
Sandpaper, files, and abrasive belts are examples of manual deburring instruments that are used to remove burrs by hand carefully. This process, while labor-intensive and time-consuming, offers fine control and works well for burr removal from surfaces of small workpieces that require a more accurate approach or from hard-to-reach regions. For example, hand deburring is common among small model builders, micro engineers, watchmakers, and jewelers.
2. MECHANICAL DEBURRING
Utilizing tools and machinery, mechanical deburring eliminates burrs from metal components. In large-scale manufacturing processes, when a massive volume of parts has to be deburred, this is a standard procedure.
To eliminate burrs and produce a smooth finish, mechanical deburring procedures might make use of rotary tools, abrasive media, or abrasive materials.
Numerous machine tools, including vibratory deburring machines or tumble machines, which use mass finishing to treat multiple components at once, can be used for these procedures.
3. THERMAL DEBURRING
One specialized deburring approach that is commonly used on complex parts with complex geometries is thermal deburring, sometimes known as the "Burr-Off" method. It entails exposing the components to a regulated explosion within a specially-made chamber.
The heat energy produced throughout the procedure prevents burrs from forming. The burrs are removed and dislodged by the explosive mixture inside the chamber without endangering the machined surfaces. This is a very effective way to deburr small or difficult-to-reach locations.
4. ELECTROCHEMICAL DEBURRING
Using a chemical reaction to remove burrs from metal objects, electrochemical deburring is a precise and effective deburring technique. The impacted area or burr is removed with an electric current, leaving a smooth surface in its wake.
Electrochemical deburring is very useful for delicate parts and complex shapes since it removes undesirable material selectively and leaves the surrounding areas undamaged.
In fields where extreme precision and a high-quality finish are crucial, including electronics and aerospace, this technique is frequently employed.
5. ROBOTIC DEBURRING
Robotic deburring solutions are a result of recent technological breakthroughs in automation.
Robotic deburring entails performing accurate and reliable deburring operations with a robotic arm fitted with deburring instruments.
Extensive manufacturing facilities and machine shops that need to deburr quickly and precisely frequently use this technique.
The benefit of robotic deburring is higher production because the robotic arm can work continuously without needing to rest or take breaks, guaranteeing consistent quality in the final product.
DEBURRING TOOLS: HOW TO GET A SMOOTH SURFACE
Depending on the deburring technique, several tools are utilized to remove burrs efficiently and produce a high-quality finish. Let's examine a few standard instruments used in various deburring procedures.
1. MANUAL TOOLS
When deburring by hand, hand tools like files, scrapers, and sandpaper are frequently used to remove burrs. Hand tools give users excellent control and make it possible for them to access tight spaces or complicated locations.
Hand deburring is possible even in small-scale operations thanks to these affordable, easily accessible, and simple instruments.
Sandpaper, grinding pads, abrasive cloths, and an abrasive diamond hand pad can all be used to smooth flat surfaces quickly.
2. ABRASIVE BELTS
In mechanical deburring techniques, burrs are removed from parts by passing them through or up against a spinning abrasive belt. This is where abrasive belts come into play.
This method, which is frequently automated, enables the speedy deburring of a large number of parts. Different grit sizes of abrasive belts are offered to achieve varying degrees of surface polish.
3. ROTARY TOOLS
Mechanical deburring is often accomplished with rotary tools like grinding stones, carbide burrs, and diamond burrs. These instruments, which are fast and effective at removing burrs, are mounted on a rotating machine.
Specifically, carbide burrs are renowned for their resilience and capacity to handle the most difficult burrs on a metal surface.
The strength and ability of diamond burrs to smooth out burrs on a glass, ceramic, or stone surface are well recognized. The ability to access intricate regions is made possible by the diversity of rotary tools, which come in numerous sizes and shapes.
4. VIBRATORY DEBURRING MACHINES
Machines for vibratory deburring are frequently employed in mass-finishing procedures. These devices remove undesirable material by creating friction between the burrs and the abrasive media through a vibrating action. Vibratory deburring devices can produce reliable, uniform results on a variety of metal products.
5. CNC DEVICES
In the manufacturing sector, computer numerical control (CNC) machines are commonly utilized for a variety of tasks, including deburring. Accuracy and consistency can be guaranteed by programming a CNC machine to carry out precise and repeatable deburring activities. These devices are frequently used in high-precision applications and are capable of removing burrs from complex geometries utilizing carbide end mills.
SELECTING THE BEST DEBURRING TECHNIQUE FOR THE TASK
With so many deburring methods and tools at our disposal, it's critical to choose the one best suited to the demands of the particular project. When selecting the deburring procedure, keep the following things in mind:
PART MATERIAL
Because different materials require different deburring processes, the type of material being used for the item is an essential factor to take into account. Stainless steel and aluminum might need a different deburring technique than materials made of plastic, stone, glass, or ceramic.
BURR TYPE
Choosing the proper deburring technique is also heavily influenced by the type and degree of the burr. Minor burrs might need a light touch, whereas sharp burrs might need a more vigorous deburring strategy.
CONFIGURATION OF THE MACHINE
Additionally, the availability of particular deburring tools needs to be taken into account. It could be more economical and efficient to incorporate deburring into an already-existing machine setup if the specific tool or machine is already being used for other tasks.
SKILL OF THE OPERATOR
The degree of competence and process knowledge possessed by the staff or machine operator should also be taken into account. Specific deburring techniques could call for particular knowledge or expertise to guarantee the best outcomes and reduce mistakes.
PART DIMENSIONS AND SHAPE
While choosing the deburring technique, the dimensions and form of the component to be deburred should be taken into account. In comparison to smaller, more intricate pieces, more significant parts could call for a different strategy. It may also be necessary to employ particular deburring tools or processes for complex forms.
Manufacturers can select the best deburring technique to remove burrs and achieve the desired quality level for their products by carefully weighing these aspects.
Tip- Use heavy-duty industrial cleaning wipes to clean surfaces and equipment. The wipes are designed with Fiberloq technology, a unique feature that effectively traps dirt and grime, making it easy to clean surfaces without leaving any residue.
Conclusion
Deburring is an essential process in the manufacturing industry, as it removes burrs—undesirable rough edges and sharp bulges—from metal components. Burrs can negatively impact the quality, functionality, and appearance of a part. Deburring can be done by a variety of methods, including manual deburring, mechanical deburring, thermal deburring, electrochemical deburring, and robotic deburring.
The best deburring technique for a particular application will depend on factors such as the material to be deburred, the type and degree of burr, the configuration of the machine, the skill of the operator, and the dimensions and shape of the part.
By selecting the right deburring technology, manufacturers can ensure that their products are of the highest quality.